Common Manitowoc ice maker problems include insufficient ice production and unusual noises. Regular maintenance and troubleshooting can often resolve these issues.
Manitowoc ice makers are popular in commercial settings for their reliability and efficiency. However, like any appliance, they can experience problems that disrupt operations. Understanding these common issues is crucial for maintaining optimal performance. Problems such as low ice production, water leaks, or strange sounds can arise, affecting both service quality and customer satisfaction.
Identifying the root cause early can save time and money. This guide will explore the most frequent Manitowoc ice maker problems and provide practical solutions to keep your machine running smoothly. Investing in proper care ensures consistent ice supply and prolongs the life of your unit.
Common Issues With Manitowoc Ice Makers
Manitowoc ice makers are popular for their reliability. Yet, they can face some common problems. Understanding these issues can help you troubleshoot effectively.
Machine Not Producing Ice
One of the most frustrating problems is a machine that won’t produce ice. Several factors can cause this issue:
- Power Supply: Check if the machine is plugged in.
- Water Supply: Ensure the water line is connected.
- Temperature Settings: Verify that the temperature is set correctly.
- Condenser Issues: Clean the condenser to improve efficiency.
If these steps do not resolve the issue, consider the following:
- Inspect the water filter.
- Look for any ice blockages inside the machine.
- Check for error codes on the display.
Ice Quality Is Poor
Poor ice quality can ruin your drinks. Several factors contribute to this problem:
Issue | Possible Causes | Solutions |
---|---|---|
Cloudy Ice | Minerals in water | Use filtered water |
Small Ice Cubes | Low water pressure | Check water supply |
Ice Odor | Dirty components | Clean the machine regularly |
Regular maintenance is key. Clean the machine often to ensure high-quality ice. Replace filters as needed. Monitor water quality for the best results.
Troubleshooting Power Problems
Power issues can cause your Manitowoc ice maker to stop working. Identifying and fixing these problems early helps keep your machine running smoothly. Below are some easy steps to troubleshoot power issues.
Checking Power Supply
Start by inspecting the power supply. Follow these steps:
- Ensure the ice maker is plugged in securely.
- Check the outlet for any signs of damage.
- Use a multimeter to test the outlet voltage.
Here’s a quick guide to check the outlet:
Step | Action |
---|---|
1 | Unplug the machine. |
2 | Plug in another device to check the outlet. |
3 | Test voltage with a multimeter. |
Replace fuses or reset breakers if necessary. Ensure the power source is reliable.
Resetting The Machine
Sometimes, resetting your Manitowoc ice maker can solve power problems. Here’s how:
- Locate the reset button on your machine.
- Press and hold the button for 10 seconds.
- Release the button and wait for the machine to restart.
Observe the machine for any changes. Ensure it powers on properly. Resetting often clears minor glitches. Regular resets can help maintain performance.
Water-related Fixes
Water-related issues often cause problems in Manitowoc Ice Makers. Proper water flow and filtration are essential. Here are two main areas to check: ensuring adequate water flow and cleaning the water filter.
Ensuring Adequate Water Flow
Insufficient water flow can hinder ice production. Follow these steps to ensure proper water flow:
- Check the Water Supply Line: Ensure it is not kinked or blocked.
- Inspect the Water Inlet Valve: Make sure it opens correctly.
- Examine Water Pressure: The pressure should be between 20-80 PSI.
- Look for Leaks: Inspect connections and hoses for leaks.
Fixing these issues can restore the ice maker’s performance.
Cleaning The Water Filter
A dirty water filter can cause multiple problems. It may reduce water flow or affect ice quality. To clean or replace the filter, follow these steps:
- Locate the water filter in your ice maker.
- Remove the filter as per the manufacturer’s instructions.
- Rinse it under warm water to remove debris.
- Inspect for damage and replace if necessary.
- Reinstall the filter securely.
Regular cleaning improves performance and extends the ice maker’s life.
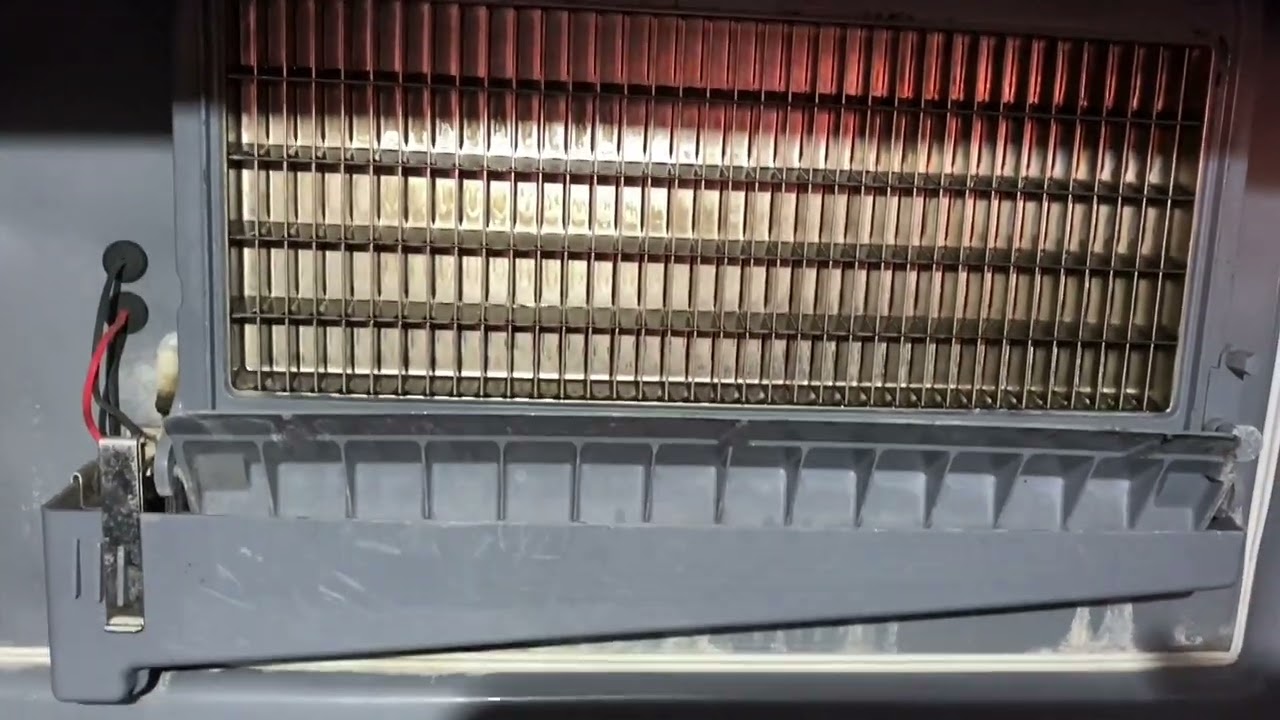
Credit: m.youtube.com
Solving Ice Production Issues
Ice production problems can disrupt your business. Manitowoc ice makers are reliable but may face issues. Understanding how to solve these problems is vital. This section covers key areas to improve ice production.
Adjusting The Ice Thickness
Ice thickness affects overall ice production. If your ice is too thin or thick, adjustments are necessary. Follow these steps to optimize ice thickness:
- Locate the thickness adjustment screw.
- Turn the screw clockwise to increase thickness.
- Turn the screw counterclockwise to decrease thickness.
Check the ice thickness regularly. Ideal thickness is about 7/8 inch. Use a ruler to measure accurately.
Optimizing The Harvest Cycle
The harvest cycle is crucial for ice production. A proper cycle ensures maximum efficiency. Here’s how to optimize it:
- Inspect the water supply. Ensure it flows freely.
- Clean the evaporator plate. Remove any buildup.
- Check the thermostat settings. They should match manufacturer guidelines.
- Monitor the cycle time. Adjust for faster or slower cycles as needed.
Regular maintenance improves the harvest cycle. Schedule routine checks to prevent issues.
Temperature Control Tips
Proper temperature control is vital for your Manitowoc ice maker. It ensures efficient ice production and maintains ice quality. Here are some effective tips to manage temperature effectively.
Monitoring Ambient Temperature
Check the room temperature where the ice maker operates. The ideal ambient temperature should range between 50°F and 100°F. Higher temperatures can impact ice production.
- Use a thermometer to monitor the room.
- Avoid placing the unit near heat sources.
- Keep windows and doors closed to maintain stable temperature.
Adjusting The Thermostat
Adjusting the thermostat can enhance ice maker performance. Follow these simple steps:
- Locate the thermostat dial or control panel.
- Set the temperature to the recommended level.
- Wait 24 hours to check ice production.
If ice production is low, lower the temperature setting slightly. Ensure the thermostat is accurate. Regularly check for any malfunctions.
Temperature Setting | Ice Production Level |
---|---|
Low (below 0°F) | Excessive ice, possible jams |
Optimal (0°F to 10°F) | Ideal ice production |
High (above 10°F) | Reduced ice production |
Cleaning And Maintenance
Proper cleaning and maintenance keep your Manitowoc Ice Maker running smoothly. Regular care prevents common problems. It ensures the ice produced is safe and clean.
Regular Cleaning Schedule
Establishing a regular cleaning schedule is essential. This helps prevent buildup and keeps the machine in top shape. Follow these steps for effective cleaning:
- Clean the ice maker every six months.
- Inspect for any signs of mold or mildew.
- Check and clean air filters regularly.
- Flush the water system to remove debris.
Use the following table to track your cleaning schedule:
Task | Frequency | Last Done |
---|---|---|
General Cleaning | Every 6 months | [Insert Date] |
Filter Inspection | Monthly | [Insert Date] |
Water System Flush | Every 3 months | [Insert Date] |
Sanitizing Ice Storage Bins
Sanitizing ice storage bins is crucial. This step prevents contamination. Follow these simple steps to sanitize:
- Remove ice from the bin.
- Use a mild detergent mixed with warm water.
- Scrub the interior surfaces thoroughly.
- Rinse with clean water to remove any soap residue.
- Apply a food-safe sanitizer.
- Allow the bin to air dry completely before refilling.
Regular sanitization keeps your ice clean and safe to use. Follow these steps consistently for the best results.
When To Call A Professional
Manitowoc ice makers are reliable. Yet, they can experience problems. Knowing when to call a professional is crucial. This decision can save time and money.
Recognizing Complex Issues
Some problems are easy to fix. Others require professional help. Here are signs to watch for:
- Strange noises: Grinding, clanking, or buzzing sounds.
- Water leaks: Puddles forming under the machine.
- Ice quality: Cloudy, discolored, or poorly formed ice.
- Frequent breakdowns: Regular issues despite DIY fixes.
- Error codes: Displayed on the control panel.
These signs indicate a complex issue. DIY fixes may not resolve them.
Finding Qualified Technicians
Choosing the right technician is important. Here are steps to find qualified help:
- Search for local repair services.
- Check online reviews and ratings.
- Ask for recommendations from friends.
- Verify the technician’s experience with Manitowoc products.
- Request a quote before any work starts.
Qualified technicians ensure proper repairs. This helps your ice maker last longer.

Credit: www.culinarydepotinc.com
Preventive Measures For Longevity
Maintaining your Manitowoc ice maker is essential for its performance. Regular care can prevent common issues. Follow these preventive measures to extend its lifespan.
Routine Inspections
Regular inspections help identify problems early. Check these components:
- Water filter: Replace it every six months.
- Condenser coils: Clean them every three months.
- Ice bin: Inspect for cracks or damage.
- Drain line: Ensure it’s clear of blockages.
Schedule inspections every few months. Document any issues found. This will help in future maintenance.
Implementing Usage Best Practices
Proper usage extends the life of your ice maker. Follow these best practices:
- Keep the unit in a cool, dry place.
- Avoid overloading the ice bin.
- Use clean water for ice production.
- Turn off the machine during long periods of inactivity.
These steps help prevent unnecessary wear and tear. Regular maintenance ensures optimal performance.

Credit: www.reddit.com
Frequently Asked Questions
What Are Common Manitowoc Ice Maker Problems?
Common issues include poor ice production, ice not harvesting, and unusual noises during operation.
How To Troubleshoot Manitowoc Ice Maker Issues?
Check the water supply, ensure proper temperature settings, and inspect for blockages in the ice bin.
Why Is My Manitowoc Ice Maker Leaking?
Leaks often result from clogged drainage or damaged seals. Inspect these areas for potential issues.
What To Do If Ice Is Cloudy?
Cloudy ice usually indicates impurities in the water. Use filtered water for clearer ice production.
How To Reset A Manitowoc Ice Maker?
Locate the reset button on the machine, press it, and wait for the unit to restart its cycle.
Conclusion
Manitowoc ice makers can face various issues that disrupt their performance. Regular maintenance and timely troubleshooting are essential for optimal operation. Understanding common problems helps you address them effectively. By staying informed, you can ensure your ice maker runs smoothly, providing you with the ice you need without interruptions.