Loader control valve problems often arise from leaks, wear, or incorrect settings. These issues can lead to poor loader performance and increased downtime.
Loader control valves play a crucial role in managing hydraulic fluid flow, impacting a machine’s efficiency and safety. Issues such as leaks or blockages can significantly hinder operations, making it essential to identify and resolve these problems quickly. Regular maintenance and timely inspections can prevent many common valve issues.
Understanding the symptoms of a malfunctioning valve helps in diagnosing the problem early. Operators should be aware of signs like erratic movements or unresponsive controls. Addressing these concerns promptly can save time and reduce repair costs, ensuring your loader operates smoothly and effectively.
Common Loader Control Valve Issues
Loader control valves are essential for smooth operation. Problems can lead to inefficiency and costly repairs. Here are some common issues faced with loader control valves.
Leaks And Their Causes
Leaks in loader control valves can disrupt functionality. Understanding the causes helps in quick resolution.
- Worn Seals: Over time, seals can wear out, causing leaks.
- Corroded Components: Rust and corrosion weaken valve integrity.
- Poor Installation: Incorrectly fitted valves can lead to leaks.
- High Pressure: Excessive pressure can force fluids out of weak spots.
Cause | Description |
---|---|
Worn Seals | Seals lose their effectiveness over time. |
Corroded Components | Rusty parts can lead to failures. |
Poor Installation | Incorrect fitting increases leak risks. |
High Pressure | Too much pressure can rupture seals. |
Sticking Valves And Solutions
Sticking valves create operational challenges. Identifying the problem helps find solutions.
- Dirty Oil: Contaminated oil can cause sticking.
- Wear and Tear: Regular use leads to wear on valve components.
- Improper Alignment: Misalignment can prevent smooth operation.
- Temperature Fluctuations: Extreme temperatures affect valve movement.
Here are some solutions to address sticking valves:
- Regularly replace hydraulic oil.
- Perform routine maintenance checks.
- Ensure proper alignment during installation.
- Use temperature control measures.
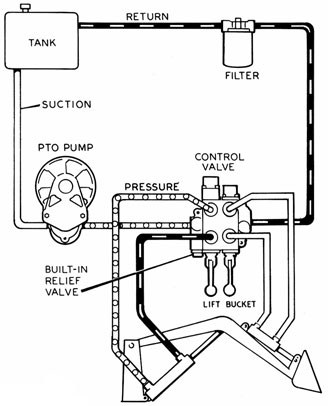
Credit: crossmfg.com
Diagnosing Loader Valve Problems
Diagnosing loader valve problems is crucial for efficient operation. Early detection can save time and money. Recognizing symptoms helps in addressing issues quickly. Understanding the tools and techniques aids in effective diagnosis.
Initial Symptoms And Signs
Loader valve problems often present clear symptoms. Look for these initial signs:
- Slow Operation: Loader functions move slower than usual.
- Unresponsive Controls: Controls fail to respond properly.
- Leaking Fluid: Fluid leaks around the valve area.
- Noisy Operation: Unusual sounds during operation.
- Erratic Movement: Sudden jerks or unexpected stops.
Tools And Techniques For Diagnosis
Utilize the right tools for diagnosing loader valve issues. Here are some recommended tools:
Tool | Purpose |
---|---|
Pressure Gauge | Measures hydraulic pressure levels. |
Fluid Tester | Checks fluid quality and contamination. |
Wrench Set | For tightening or loosening fittings. |
Digital Multimeter | Tests electrical connections. |
Use these techniques for effective diagnosis:
- Inspect the hydraulic fluid level.
- Check for visible leaks around the valve.
- Test the hydraulic pressure with a gauge.
- Listen for abnormal sounds during operation.
- Examine electrical connections for faults.
Quick Fixes For Loader Valve Malfunctions
Loader valve malfunctions can disrupt operations. Quick fixes can save time and money. Here are some simple solutions to common issues.
Sealing Leaks Temporarily
Leaks in loader valves can lead to performance issues. Sealing them quickly is crucial. Use these steps for a temporary fix:
- Identify the Leak: Look for oil spots or wet areas.
- Clean the Area: Use a rag to remove dirt and debris.
- Apply Epoxy Putty: Mold the putty around the leak.
- Allow to Cure: Wait for the putty to harden as per instructions.
- Monitor: Check for any new leaks after the fix.
Unsticking Valves Without Professional Help
Stuck valves can cause loader malfunctions. You can unstick them without calling a pro. Follow these steps:
- Inspect the Valve: Look for dirt or damage.
- Use a Hammer: Tap the valve gently with a rubber mallet.
- Apply Penetrating Oil: Spray oil on the valve and let it sit.
- Move the Valve: Gently try to operate it manually.
- Test the Loader: Run the loader to ensure smooth operation.
These quick fixes can help keep your loader functioning well. Regular maintenance will prevent future problems.
Preventative Maintenance Strategies
Effective maintenance can prevent loader control valve problems. Regular care helps maintain efficiency and extend the lifespan of your equipment. Implementing simple strategies can save time and money.
Regular Inspection Routines
Regular inspections are vital for identifying issues early. Follow these steps for effective inspections:
- Check for visible leaks around the valve.
- Inspect hoses for wear and tear.
- Look for unusual noises during operation.
- Monitor fluid levels regularly.
Schedule inspections monthly or quarterly. Keep a maintenance log. Record any findings to track changes over time.
Lubrication And Cleaning Tips
Proper lubrication reduces wear on moving parts. Clean components to prevent dirt buildup. Follow these tips:
- Use the manufacturer-recommended lubricant.
- Apply grease to all pivot points.
- Wipe down the valve and surrounding areas.
- Clean filters as needed to ensure proper flow.
Regular lubrication and cleaning can prevent many valve issues. Set a schedule to ensure these tasks are not overlooked.
Task | Frequency | Notes |
---|---|---|
Inspection | Monthly | Look for leaks and wear. |
Lubrication | Every 3 months | Use recommended lubricants. |
Cleaning | Monthly | Remove dirt and debris. |
Hydraulic Fluid Management
Proper hydraulic fluid management is vital for loader control valves. The right fluid ensures smooth operation and long-lasting performance. Poor fluid management can lead to serious problems.
Choosing The Right Fluid
Selecting the correct hydraulic fluid is crucial. The fluid impacts the system’s efficiency and reliability. Consider the following factors:
- Viscosity: Choose fluid with the right thickness.
- Temperature Range: Ensure fluid performs well in various temperatures.
- Compatibility: Check if the fluid works with your system’s components.
- Additives: Look for fluids with anti-wear and anti-foam properties.
Refer to the table below for common hydraulic fluids:
Fluid Type | Viscosity (cSt at 40°C) | Temperature Range (°C) |
---|---|---|
AW 32 | 32 | -20 to 68 |
AW 46 | 46 | -15 to 70 |
AW 68 | 68 | -10 to 75 |
Fluid Change And System Flush
Regular fluid changes are essential for maintaining performance. Old fluid can contain contaminants that harm the system.
- Check Fluid Condition: Look for discoloration or debris.
- Drain Old Fluid: Ensure complete removal.
- Flush the System: Use a flush solution to clean.
- Refill with New Fluid: Use the correct type and amount.
Follow the manufacturer’s guidelines for frequency. Regular maintenance prevents costly repairs and extends your loader’s life.
Professional Vs. Diy Repair Approaches
Loader control valves are crucial for smooth operation. Repairing them can be tricky. Deciding between professional help or DIY can save money or lead to mistakes. Understanding both approaches is vital for effective repair.
When To Call The Experts
Not all loader control valve issues are simple. Here are signs that you should contact a professional:
- Complex Problems: If the valve shows multiple issues.
- Safety Risks: If repair could harm you or others.
- Time Constraints: When you need the loader fixed quickly.
- Warranty Concerns: If repairs might void your warranty.
Experts have the right tools and experience. They can diagnose problems accurately. This often leads to faster and safer repairs.
Diy Repair Safety Tips
Choosing to repair the loader control valve yourself can be rewarding. Follow these safety tips:
- Read the Manual: Understand your loader’s specifications.
- Wear Safety Gear: Use gloves, goggles, and a hard hat.
- Disconnect Power: Always turn off power before starting.
- Use Proper Tools: Ensure you have the right tools for the job.
- Work in a Safe Area: Choose a clean, well-lit space.
Take breaks and don’t rush your work. A careful approach prevents mistakes.
Upgrading Your Loader Valve System
Upgrading your loader valve system can enhance performance and efficiency. Old valves may cause issues. A new system ensures better operation and reduces downtime. Understanding when to upgrade is key to maintaining productivity.
Signs You Need An Upgrade
- Frequent Leaks: Noticeable hydraulic fluid leaks.
- Inconsistent Performance: Irregular lifting or lowering speeds.
- Unusual Noises: Grinding or hissing sounds during operation.
- Increased Downtime: More time spent on repairs than on work.
- Old Age: Valves older than 10 years may need replacement.
Options And Considerations
Many options exist for upgrading your loader valve system. Consider the following:
Option | Description | Pros | Cons |
---|---|---|---|
New Valve Assembly | Complete replacement of the old system. |
|
|
Rebuild Existing Valve | Fixing parts of the current valve. |
|
|
Upgrade Control System | Enhancing the control interface of the valve. |
|
|
Evaluate your needs carefully. Choose an option that suits your budget and goals.
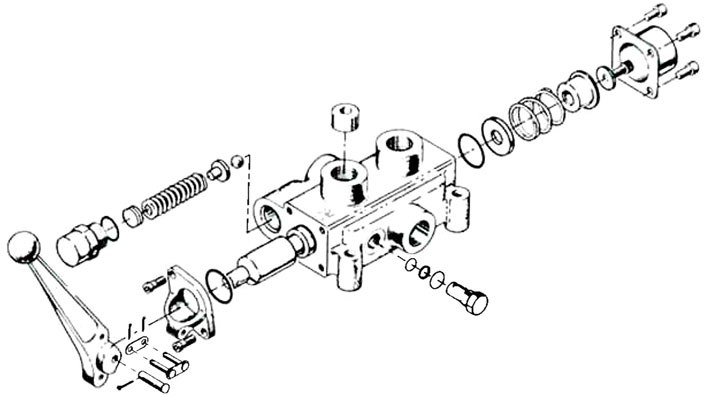
Credit: crossmfg.com
Troubleshooting Guide
Loader control valve problems can disrupt your work. Identifying the issue early helps in saving time and money. This troubleshooting guide provides clear steps for diagnosing common issues.
Common Questions Answered
Here are some frequent questions about loader control valve issues:
- What are the signs of a faulty valve?
- Unresponsive loader movements.
- Leaking hydraulic fluid.
- Unusual noises during operation.
- Can I fix it myself?
- Yes, many minor issues are DIY-friendly.
- Always follow safety guidelines.
- How often should I check the valve?
- Inspect regularly, especially before heavy use.
- Check after any major repairs.
When To Seek Further Help
Sometimes, issues may need professional intervention. Here are signs to look for:
- Persistent problems: If issues continue despite your fixes.
- Severe leaks: Large leaks can signal major issues.
- Strange noises: Unusual sounds could indicate serious damage.
Consult a professional mechanic if you encounter these signs. They have the tools and experience to diagnose complex issues.
Credit: www.tractorbynet.com
Frequently Asked Questions
What Are Common Loader Control Valve Issues?
Common issues include leaks, erratic operation, and slow response times, which can hinder loader performance and efficiency.
How To Diagnose Loader Control Valve Problems?
Check for fluid leaks, inspect valve seals, and test hydraulic pressure to identify issues effectively and accurately.
Can A Faulty Valve Affect Loader Performance?
Yes, a faulty control valve can lead to reduced power, slow operation, and increased wear on components.
How To Maintain A Loader Control Valve?
Regularly inspect seals, change hydraulic fluid, and clean filters to ensure optimal performance and longevity of the valve.
What Are Signs Of A Failing Control Valve?
Signs include unusual noises, inconsistent hydraulic response, and fluid leaks, indicating the need for immediate attention and repair.
Conclusion
Loader control valve issues can significantly impact equipment performance. Regular maintenance and timely repairs are essential to avoid costly downtime. Understanding the common problems helps operators take proactive measures. By addressing these concerns early, you can ensure your loader operates efficiently and reliably for years to come.
Stay informed and act swiftly.